Equipment Overview& Equipment Details
Equipment Details
Make, Model & Classification
Name | Baler |
Model | Model 6000 |
Classification | Baling , Compacting/Compressing |
Operations
Description or Purpose | Pneumatic powered stainless steel 1-5 LTR plastic bottle compactor baler, this is a bench top model that will crush all plastic bottles up to 5 LTRS plus #10 caterers steel cans. |
Operating Principles | Very easy to use baler, handle down to operate, handle up to disengage, 5 second cycle times, bale 70 x 2Ltr milk bottles in 3-4 minutes, average 14 x volume reduction. Very safe to use, door cannot be opened during operation or strapping of the bale. |
Additional Information | Manufactured from 304 grade stainless steel to last and provide maximum corrosion resistance, crushing force 3.2 tonnes at 9 BAR, baler has a gravity locking system to keep crushed bottles down on every cycle. |
Photograph
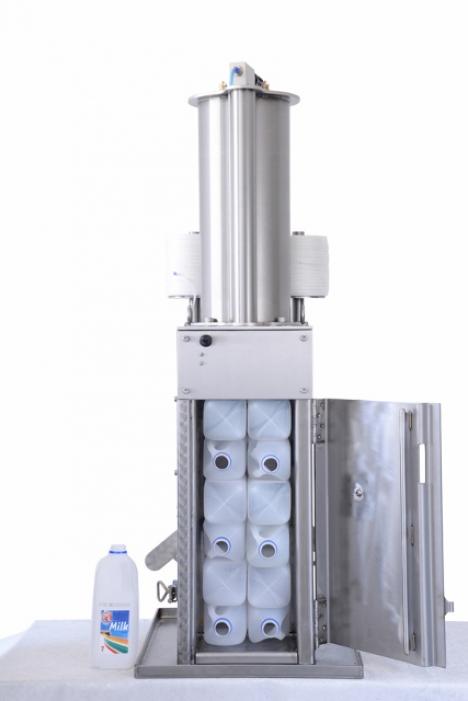
Recyclables Processed & Productivity
Recyclables Processed
Target Recyclables and Productivity Rates
Recyclable Type | Productivity - Loading Rate (kg per hour) |
Processing Capacity - Treatment (kg per week) |
Storage Capacity (kg per batch) |
Operating Life (machine hrs) |
|
---|---|---|---|---|---|
![]() |
Food Organics | ||||
![]() |
Other Organics (garden etc.) | ||||
![]() |
Flexible Plastic | 150 | 3000 | 8 | 50000 |
![]() |
Rigid Plastic | 95 | 2100 | 8 | 50000 |
![]() |
Mixed Plastics | 95 | 2100 | 8 | 50000 |
![]() |
Expanded Polystyrene | ||||
![]() |
Glass | ||||
![]() |
Paper | ||||
![]() |
Cardboard | ||||
![]() |
Mixed Paper & Cardboard | ||||
![]() |
Timber | ||||
![]() |
Other Recyclable |
Productivity
Life Expectancy
Operating Life - Years | 40 |
Level of Automation
Operating Mode | Batch |
Degree of Automation | Not automated - operator involvement required throughout process |
Labour Requirements
Number of Operators | 1 |
Operator Time (per cycle in mins.) |
4 |
Consumables Required
Consumables | none |
Service Requirements
Service Freq. (Tonnes) | |
Service Freq. (Months) | 12 |
Downtime per Service (hours) | 1 |
Periodic Cleaning Requirements
Periodic Cleaning | Clean & wipe down weekly |
Loading & Unloading Equipment
Manual Handling Loading | Manual |
Manual Handling Unloading | Manual |
Work Health and Safety & Permitting
Work Health and Safety
Training
Operator Training Requirements | Familiarisation induction - by OEM/supplier |
Personal Protective Equipment
![]() |
Head - Hard Hat |
![]() |
Eyes - Glasses |
![]() |
Breathing - Mask or Respirator |
![]() |
Hands - Gloves |
![]() |
Feet - Industrial Footwear |
![]() |
Visibility - Hi-viz Clothing |
![]() |
Other PPE |
Training Material
![]() |
Printed |
![]() |
Video/DVD |
![]() |
Web-based |
![]() |
Other |
Fencing & Enclosures
![]() |
Fencing |
![]() |
Bunding |
![]() |
Floor Reinforcing |
![]() |
Covers or Shielding |
![]() |
Other |
Approvals Related to Use of Output
Important Note on Composting in NSW
In NSW, applying waste to land – including a processed waste such as compost - or using it as a fuel may trigger various regulatory requirements. Depending on the proposed use you may be required to comply with a Resource Recovery Exemption or need to hold an environment protection licence, and pay the waste levy.
While there is a Compost Exemption (2014) it is important to note that drying or dehydrating food waste, or any other compostable waste, is specifically excluded from consideration under this exemption. Drying or dehydrating equipment uses externally supplied energy to heat and ventilate food waste or any other compostable waste in order to rapidly dry the waste material over a short time period (typically 24 to 48 hours), either with or without the addition of an inoculum. If you are interested in this type of equipment you should refer to the resource recovery exemptions for information on lawful use of outputs.
If it is intended to use the material as a fuel, it must comply with the NSW Energy from Waste Policy Statement. http://www.epa.nsw.gov.au/waste/140056enfromwasteps.htm
Installation Specifications
Installation Specifications
Utilities
![]() |
Power | Volts | |
![]() |
Water | KPa | l/min |
![]() |
Sewer | l/min | |
![]() |
Compressed Air | 800 KPa | CuM/min |
![]() |
Gas | Kjoule/hr |
Dimensions
Length | 60 cm |
Width | 50 cm |
Height | 130 cm |
Footprint | 0.5 sq.m |
Weight | 180 kg |
Lateral clearance | 100 cm |
Overhead clearance | 10 cm |
Service Offering
![]() |
Supply |
![]() |
Installation |
![]() |
Maintenance |
![]() |
Product Uplift |
![]() |
Training |
![]() |
Other |
In-Feed & Out-Feed Characteristics
In-Feed Characteristics
Acceptable In-feed Characteristics
![]() |
Loose |
![]() |
Bundled |
![]() |
Tied |
![]() |
Wet |
![]() |
Dry |
![]() |
Shredded |
![]() |
Lightly Soiled |
![]() |
Heavily Soiled |
![]() |
Other |
Exclusions
Excluded Materials | Glass |
Out-Feed Characteristics
Out-feed Product Characteristics - Shape
![]() |
Rectangular Prism |
![]() |
Cylindrical |
![]() |
Other |
Out-feed Product Characteristics - Container
![]() |
Bag/Sack |
![]() |
Wrapped |
![]() |
Bin |
![]() |
Other |
Out-feed Dimensions
Length | 30 cm |
Width | 25 cm |
Height | 30 cm |
Footprint | 0.1 sq.m |
Weight | 7 kg |
SG | 2.7 specific gravity |
Density | 300 kg/Cu.m |
By-product and Wastes |
Amenity and Nuisance Issues
![]() |
Noise |
![]() |
Odour |
![]() |
Vibration |
![]() |
Light |
![]() |
Heat |
![]() |
Other |
Market/Recipients
![]() |
Reprocessor |
![]() |
End Market |
![]() |
Other |
OEM & Supplier Information
OEM & Supplier Information
OEM Company Details
Company Name | Plastic Bottle Crusher Pty Ltd |
Postal Address | 5 Sandrew St Sunnybank PO Box 8123 Sunnybank |
State | QLD |
Country | Australia |
Postcode | 4109 |
Web Site | www.plasticbottlecrusher.com |
Contact Name | Paul |
Contact Telephone | +61 (0)407 011 988 |
Contact Email | contact@plasticbottlecrusher.com |
Supplier Company Details
Company Name | Plastic Bottle Crusher Pty Ltd |
Postal Address | 5 Sandrew St Sunnybank PO Box 8123 Sunnybank |
State | QLD |
Country | Australia |
Postcode | 4109 |
Web Site | www.plasticbottlecrusher.com |
Contact Name | Paul |
Contact Telephone | +61 (0)407 011 988 |
Contact Email | contact@plasticbottlecrusher.com |